DESIGN OF APCS SYSTEMS
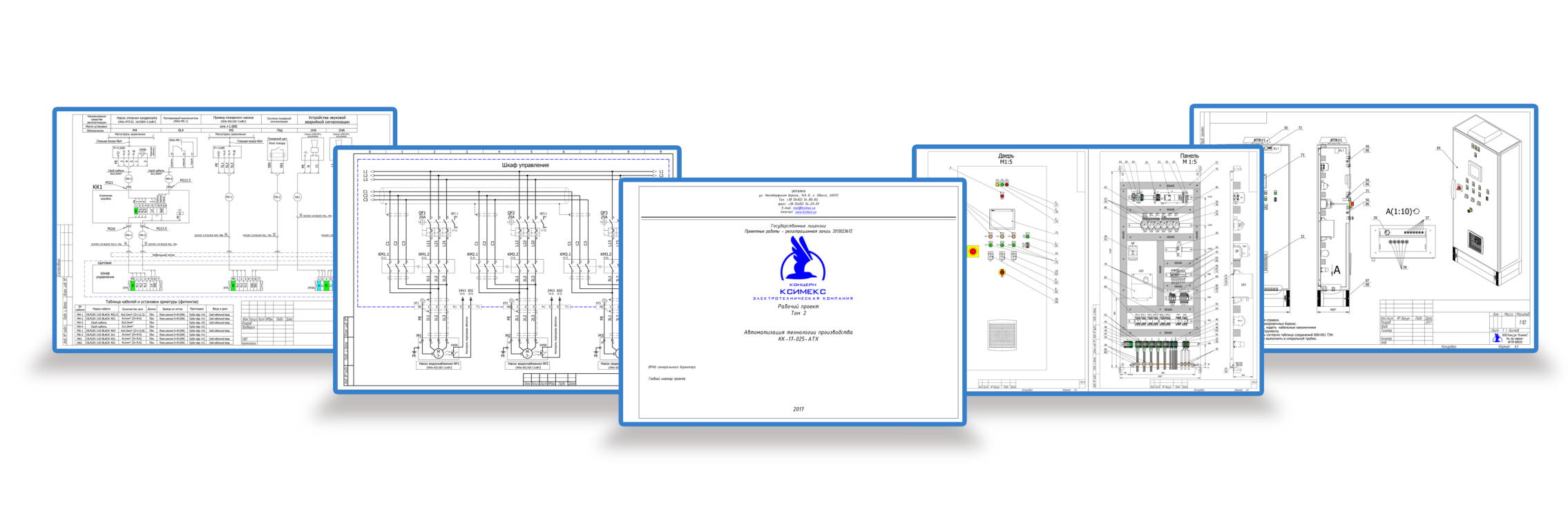
APCS – Automated Production Control Systems
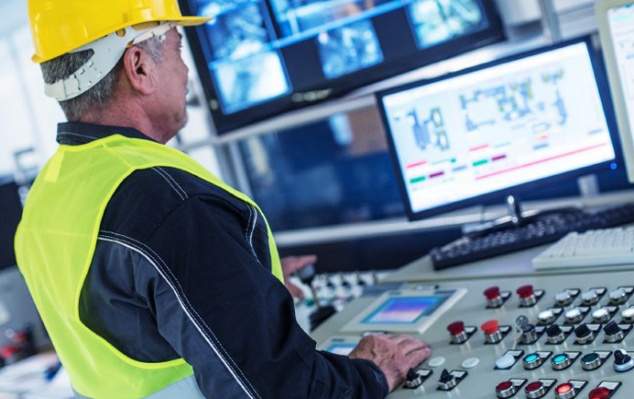
- grain elevators;
- oil extraction plants;
- food processing plants;
- oil industry enterprises;
- enterprises for transshipment of ore, coal, etc.
- Ensuring reliable and trouble-free operation of production;
- Stabilization of operational parameters of technological equipment and operating parameters of the technological process;
- Improving the qualitative and quantitative indicators of products;
- Reduced operating costs;
- Prevention of accidents;
- Automatic and automated equipment diagnostics.
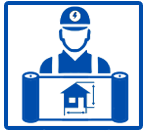
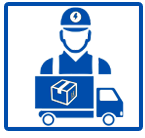
Supply of equipment
for the control system
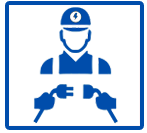
Assembly, installation and
commissioning of APCS
at the customer’s site
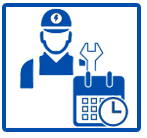
Technical and engineering support of the implemented system throughout the entire cycle
APCS DESIGN STAGES
- Justification of the need to create an automated process control system;
- Formation of target requirements for APCS;
- Object research and data collection about the automation object;
- Formation of the Customer's requirements for the APCS:
- acceptable development costs;
- commissioning and operation;
- the expected effect from the introduction of the APCS system.
- Development of the concept of the APCS;
- Development and approval of technical specifications for the creation of an automated process control system together with the customer;
- Formation of a forecast for increasing productivity, as well as economic efficiency from the introduction of APCS

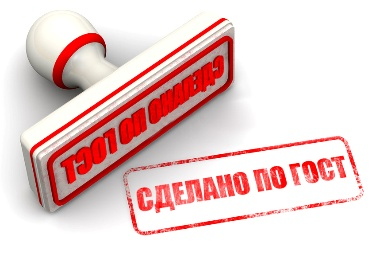
- technical specification (requirements);
- structural and functional diagrams of automation systems;
- electrical schematic diagrams;
- connection diagrams;
- assembly drawings;
- plans for the location of equipment and laying cable routes;
- Bill of materials and equipment;
- local estimate for installation and adjustment of automation equipment;
- explanatory note;
- passports and operating manuals.
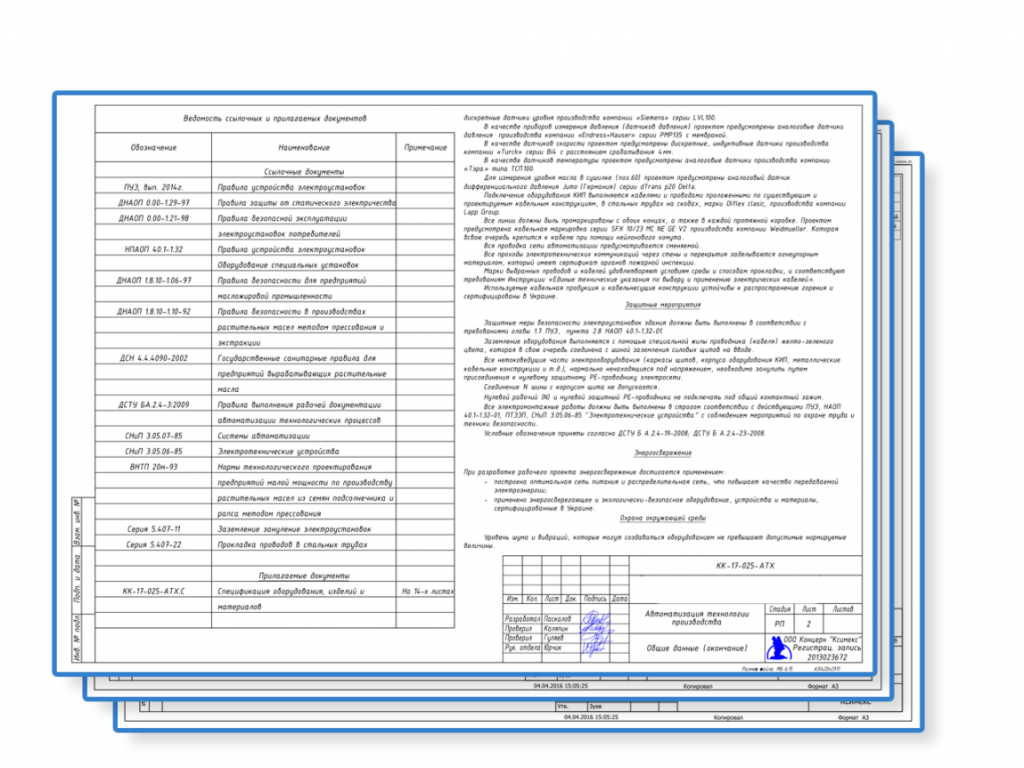
The most important document in the design is the terms of reference (TOR). TK is a document that provides comprehensive information on how exactly the work should be done. The Terms of Reference is drawn up in close cooperation between the Contractor and the Customer and must be performed in such a way that:
- The customer, after the execution of the project, received exactly the product he wanted;
- The customer spent a minimum and sufficient amount of funds on the modernization;
- The contractor completed The work for The minimum and sufficient time for this.
The structural diagram of a complex of technical means is developed at the initial stages of design and precedes the development of other types of circuits. The diagram defines the main functional parts of the product, their purpose and the relationship between them. The diagram shows the principle of operation of the product in its most general form.
The functional diagram is intended to explain the processes occurring in individual functional circuits of the product or the product as a whole. The diagram shows the functional parts of the product (elements, devices, functional groups) and the connections between them. The graphical construction of the diagram clearly reflects the sequence of functional processes occurring in the system.
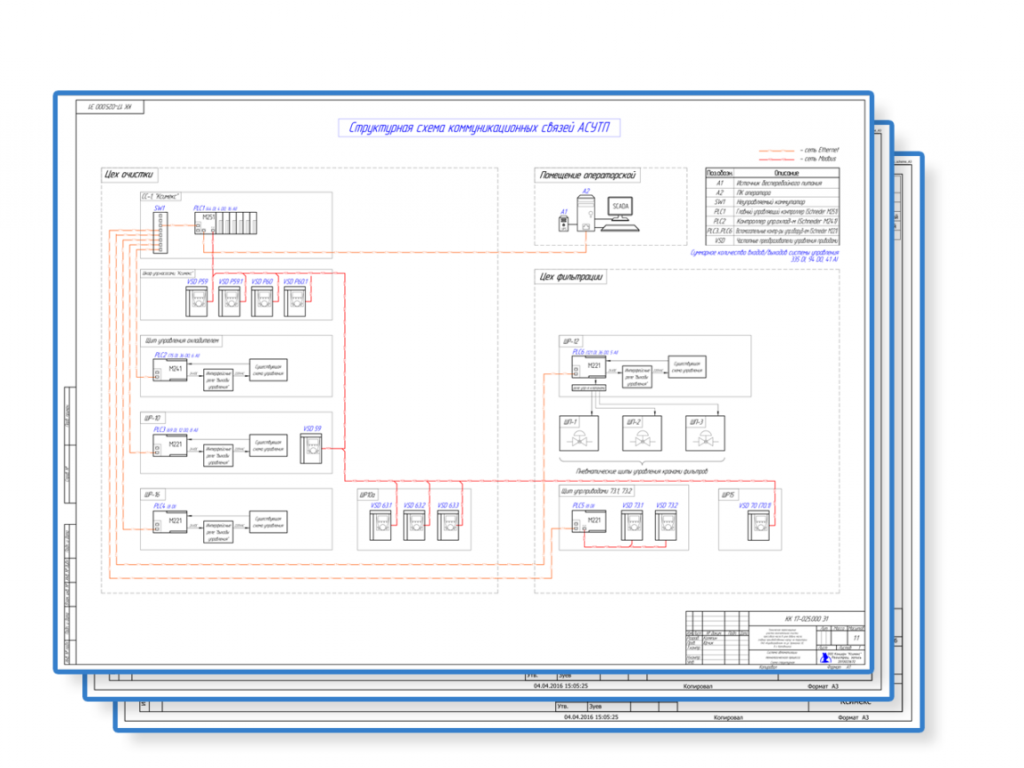
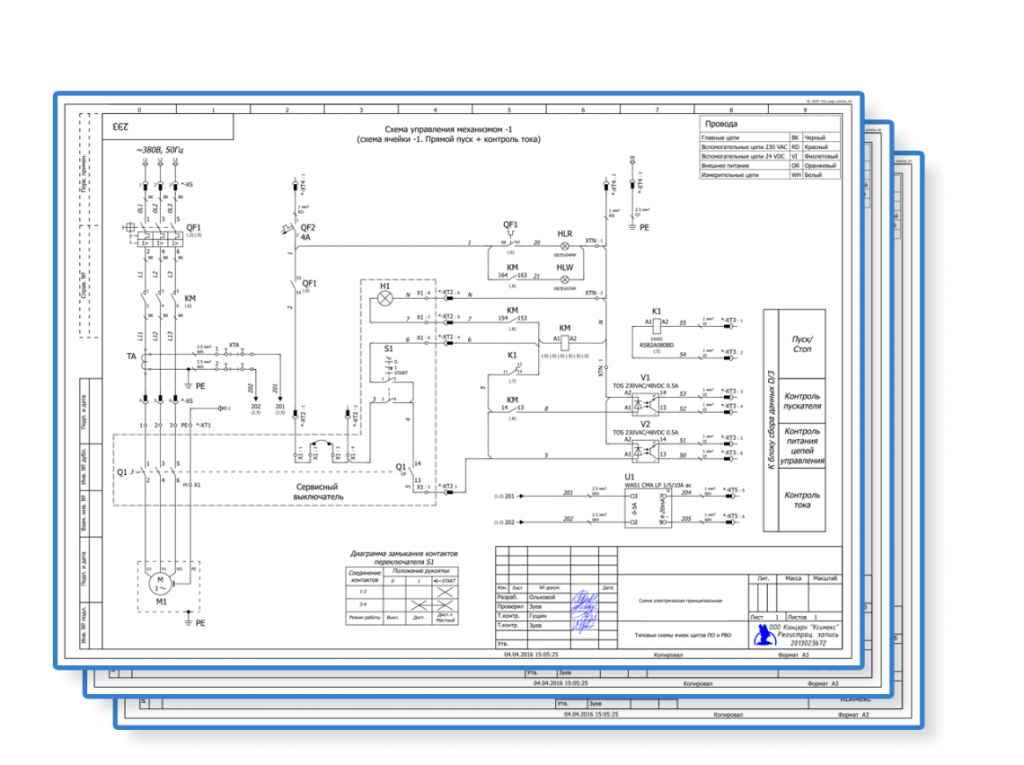
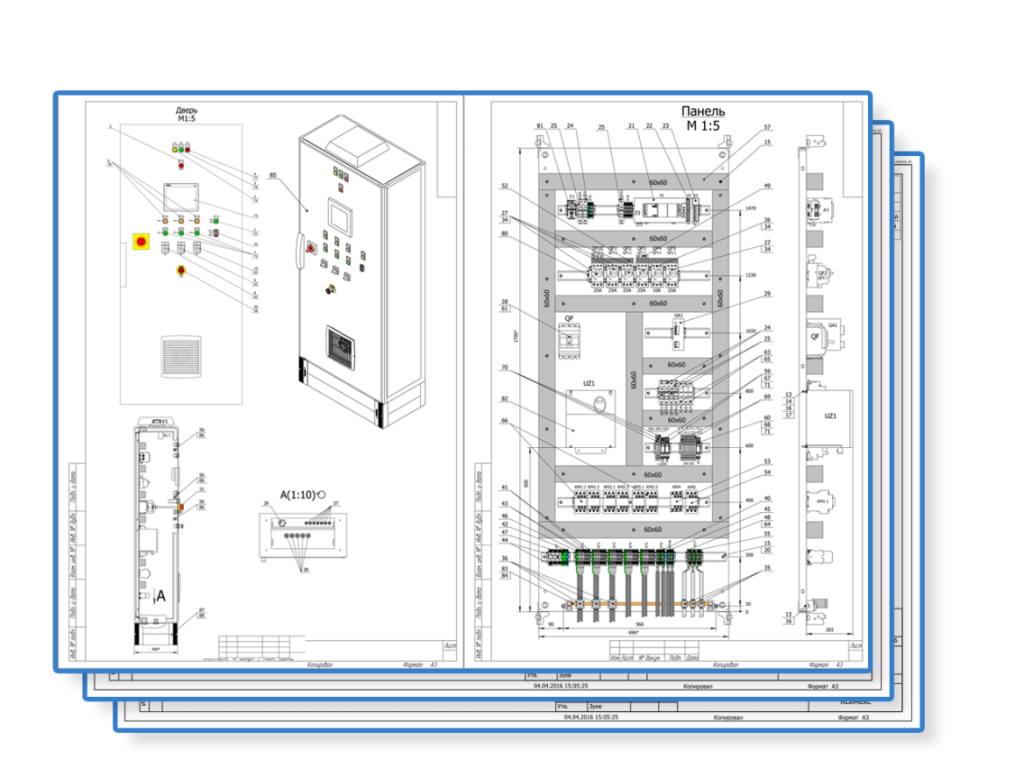
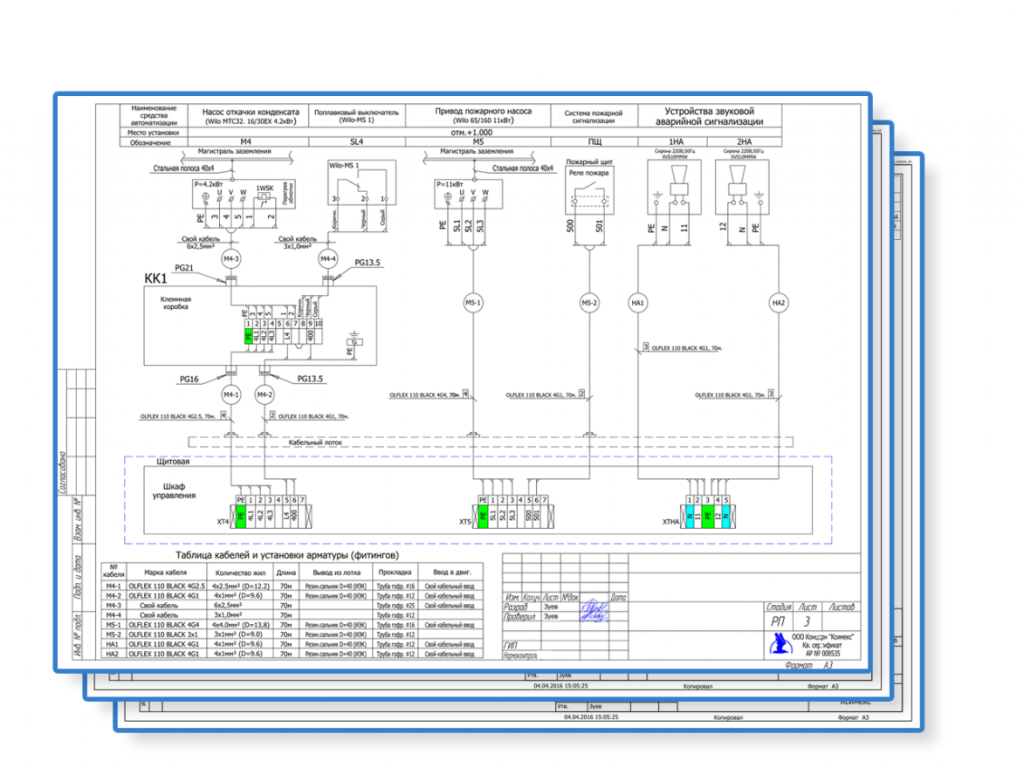
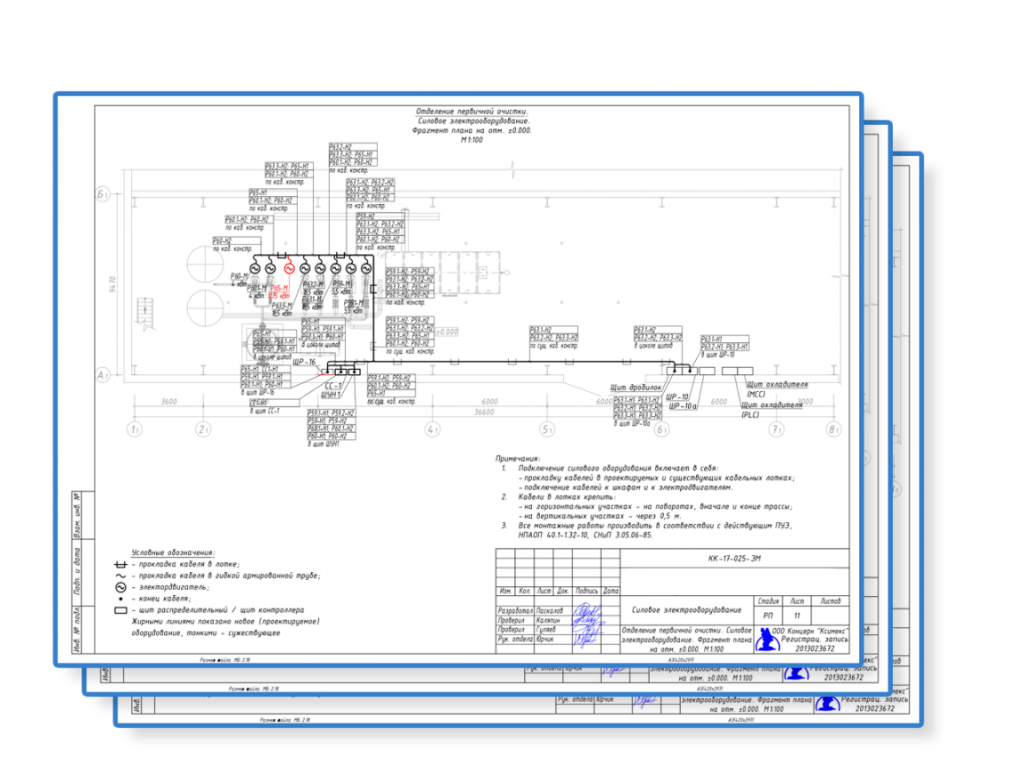
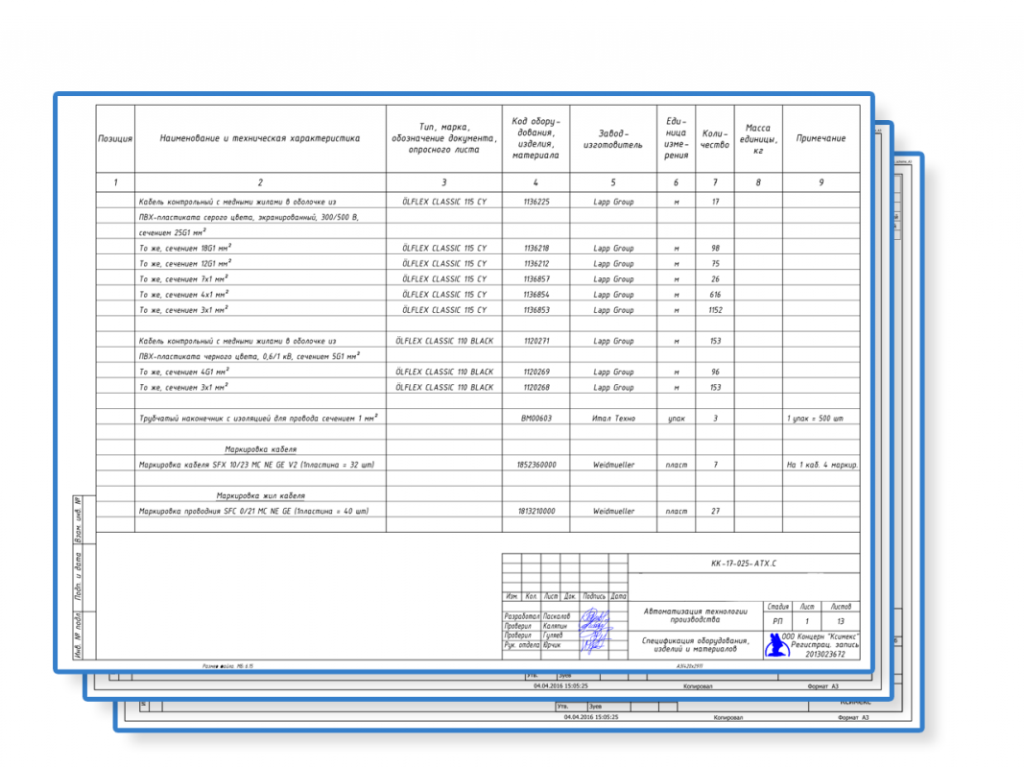
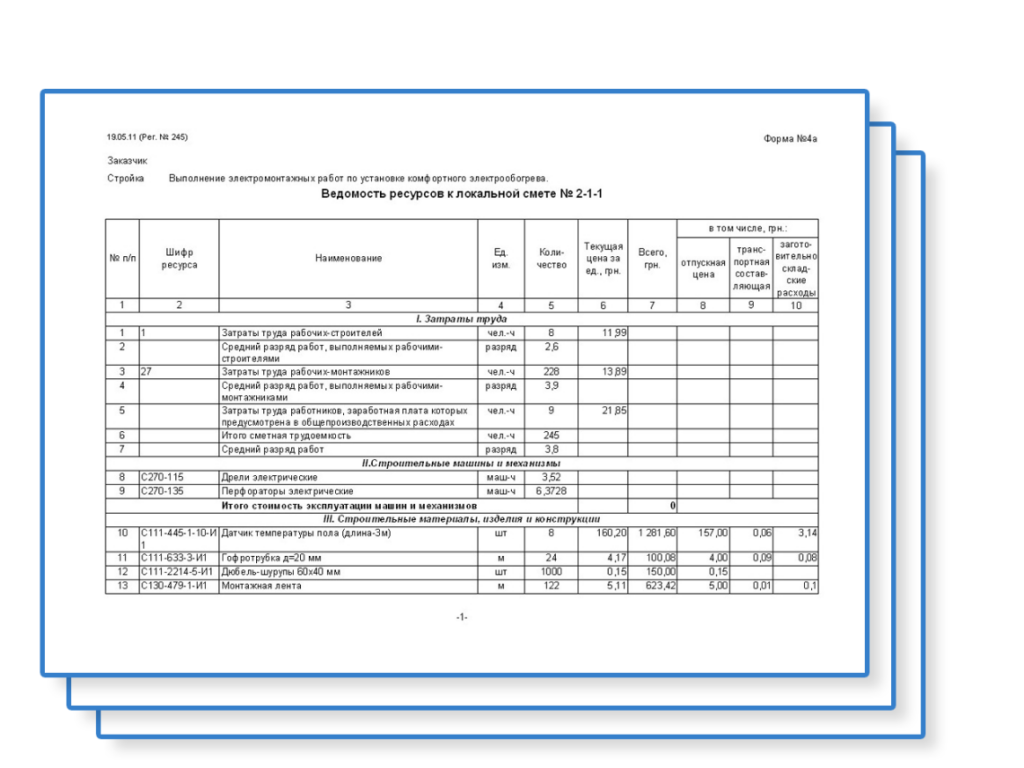
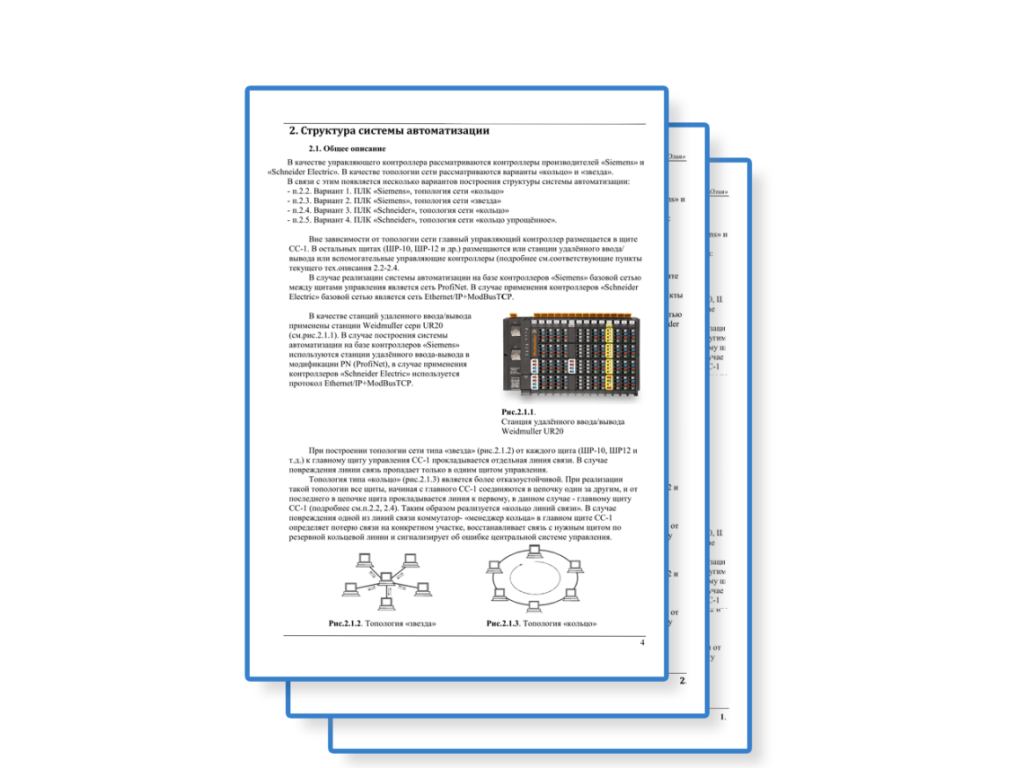
- Goals and tasks solved by the control system;
- Work principles;
- The applied system of connections between the components of the system, as well as connections with external systems;
- The types of equipment used;
- The advantages of the solutions used;
- System development opportunities for potential upgrades.
With large multi-level control systems, which include a large number of components – control panels, operator stations, data processing and storage servers, each large product is completed with a passport (PS) and an operation manual (OM). The OM describes the purpose of the product, its place and functions in the general control system, describes the purpose of the controls and indicators, and provides equipment control schemes.
In addition, the OM describes in detail the menu systems, as well as the sequence of operator actions for the correct commissioning of the equipment, correct operation throughout the entire period of operation, as well as the operator’s actions in case of emergency situations.
The operating manual is completed with the necessary diagrams, illustrations and drawings necessary for a complete understanding of the principles of correct, efficient and safe operation of the product.
In the passport for the product, the necessary marks are indicated that the device has been tested at the technical control site of the contractor, all the parameters of the product fully comply with the requirements stated in the design specification. Also in the passport for the product, the delivery set is described and the warranty obligations are indicated.
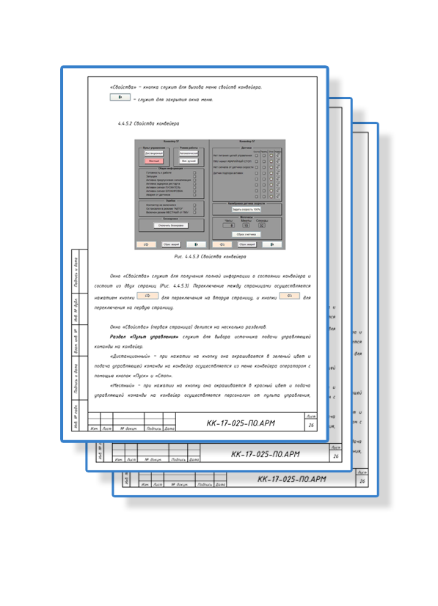