SWITCHBOARDS PRODUCTION
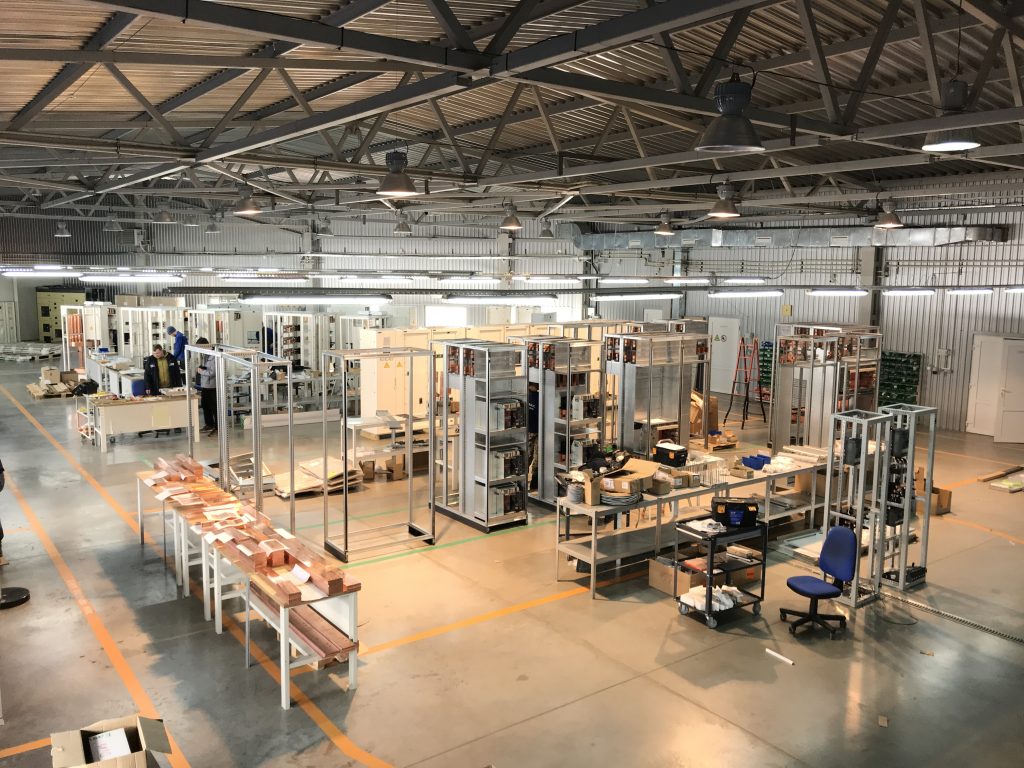
The production department of the Concern Ksimex company plays a special role, since it embodies the needs of the customer in matter, which are engineering and creatively embodied on “paper” by our designers. The more complex, innovative or large-scale task is posed, the higher the level of responsibility falls on our designers and installers.
Following the principles “If you want to do well, do it yourself” and “If the problem does not contradict the laws of physics, we will solve it”, our company has gradually and purposefully developed its own production facilities, since 1998, and to date has implemented more than 1200 projects of various purpose and complexity. Our projects are based on equipment from leading world manufacturers, in particular, our main partner, Schneider Electric.
In production and storage areas over 2000 sq. today there are several dozen highly qualified and experienced workers with all the necessary approvals and certificates.
This allows us to produce switchboard equipment for a wide variety of purposes, ranging from Automation control panels and ATS switchboards for the residential sector to power distribution boards for currents up to 7300A for industry, special purpose switchboards manufactured according to industry standards for marine applications and substation auxiliaries, including a number of nuclear power plants.
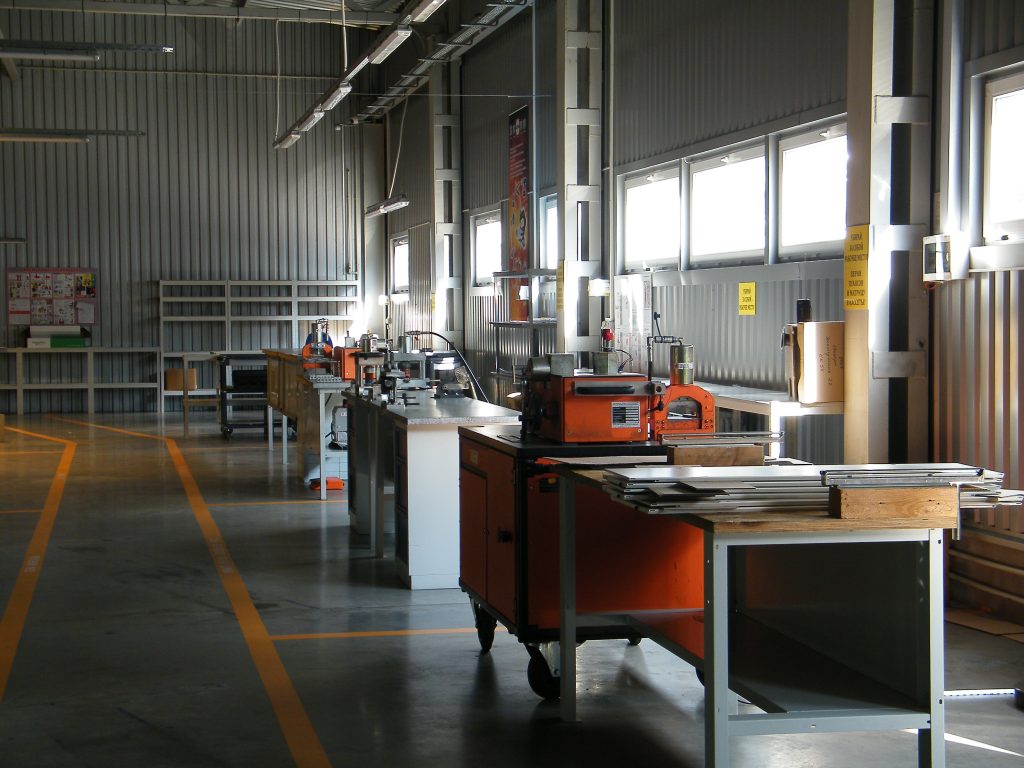
RELIABILITY AS A KEY FACTOR
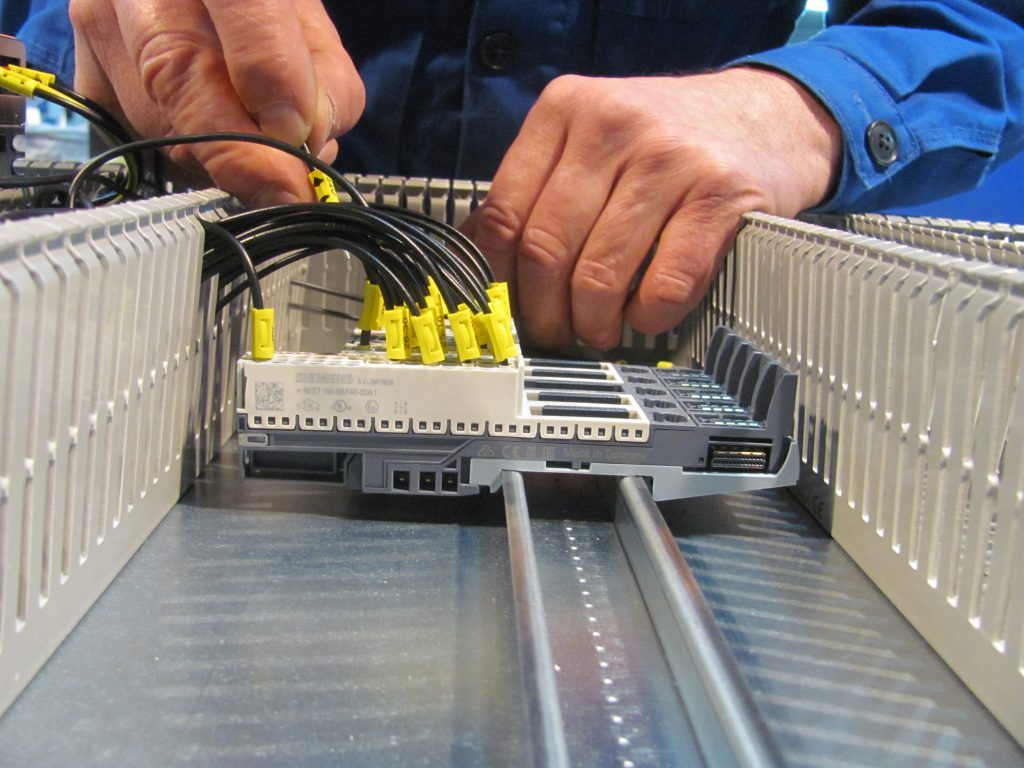
Modern electrical receivers, regardless of the field of activity (residential, industrial, or infrastructure facilities), require reliability and a guarantee of the stability of the supply network, which is mainly characterized by the purity of the supply voltage, its uninterrupted supply, and guaranteed consumer protection from external factors.
This is an extremely important aspect, since most accidents and malfunctions occur on that part of the chain, which is the last frontier. It is these areas that require reliable protective and switching equipment installed in the same reliable design solutions tested by technical laboratories.
In this regard, the design, production and commissioning of reliable electrical distribution boards and control cabinets, adapted to the required task, is not a purely formal and simple solution. “Garage assembly” of this kind of equipment does not provide protection for the end user (power consumer), with a high degree of probability it is not able to localize the accident, and moreover, the next device and device (electrical panel) following the stage of protection may not work correctly and will not cut off the emergency section, which will lead to to negative consequences both for other consumers and for oneself as a whole. Often, improper operation and inconsistency of protection circuits throughout the entire section of the line finds a “narrow”, weaker point, which may be this particular “garage shield”, which subsequently becomes a hotbed for the spread of an accident or fire both in the house and at the enterprise.
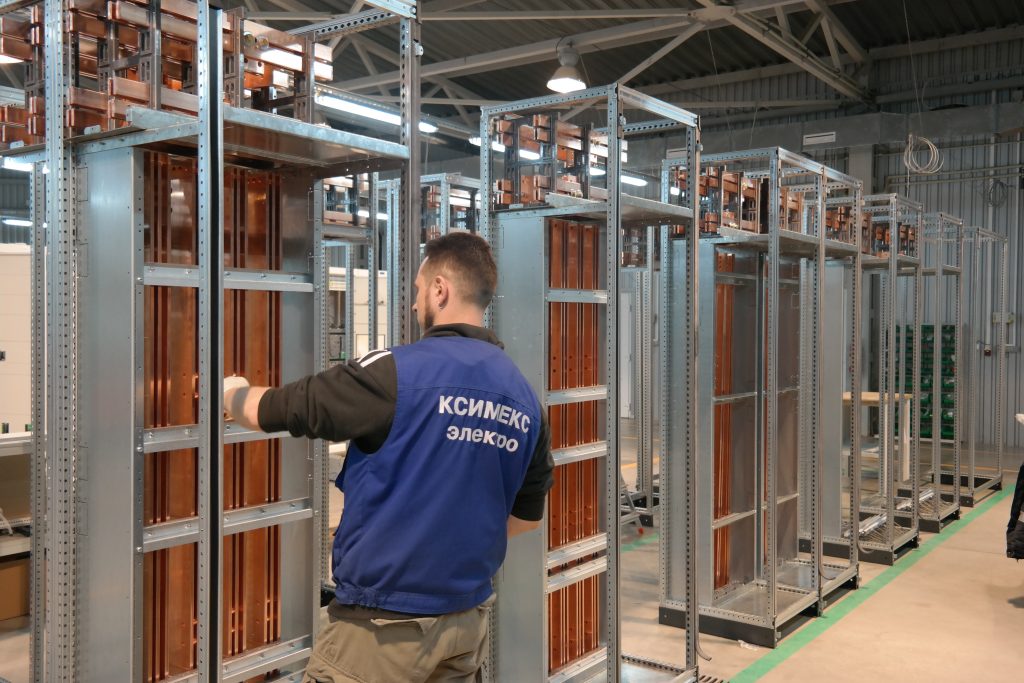
Licensed protection, distribution, and control equipment is a guarantee the stability and reliability of any industrial or residential building, and a comprehensive solution with the use of protection against electric shock is a guarantee of preserving human life. Our experience allows us to declare with confidence that we are capable of solving such problems professionally.
QUALITY CONTROL AS A GUARANTEE OF RELIABILITY AND DURABILITY
All products entering the production site are thoroughly checked. Protection and switching devices are checked for integrity, operability, and compliance with the declared electrical characteristics. The devices are checked not only through control circuits but also by loading with primary currents. The loading stands of the enterprise allow carrying out complex tests with currents up to 16000A.
Enclosures of electrical cabinets, all components required for assembly, panels, and mechanical parts undergo a primary check for external damage, and moving parts for mechanical performance.
Measurement, indication, and metering devices, after incoming control, are transferred for verification to the metrology authorities to undergo certification and obtain supporting documents. Detection of elements that do not meet the characteristics declared by the manufacturer is sent on complaints to the manufacturer for replacement with conditioned ones. This stage of verification is very important at this stage because the identified shortcomings in the configuration and operability of the equipment received cannot play a negative role in disrupting the timing of the finished product. By the time the finished product comes out, all the equipment for claims goes into production and undergoes new tests.
In the process of assembling products, the department of technical control (TC) is constantly at the assembly site, makes the detected comments to the quality control sheet during the assembly process. The TC department accepts the finished product from the installation area only if all the comments found during the assembly process have been eliminated, the elimination marks were made by the person assembling this product. The company has a permanent KPI (Key Performance Indicator) system, i.e. all detected remarks during the build process are recorded in a separate log.
This method of registration allows you to determine the degree of professional training of specialists, focus on recurring mistakes, and take measures to eliminate the latter. The personnel of the design and installation site undergo constant training and improvement both in Ukraine and at European factories and training centers. The experience of our European colleagues is being adopted in production and engineering.
The finished and tested at the assembly stage products (electrical panel) are delivered to the acceptance test zone. The access of personnel involved in the assembly of this product becomes severely restricted. The specialists of the technical control department undertake the check. Checking the finished product for compliance with design documentation, completeness, integrity of power and control circuits, a set of checks with the supply of increased voltage, checking compliance with the declared degrees of protection (IP), supplying voltage and simulating all kinds of deviations from the standard, tracking the actions of automation and output parameters depending on input data. Adjustment of protection devices to the required values of the operation of protection devices, linking the control systems of the switchboard to the required parameters of the input values. Final check of the operation of all elements included in the finished product and execution of a test report with a mark on the passage or return for revision of the equipment. Only positively passed product tests are allowed to be packaged and transported to the transport area.
Having our own certified electrical laboratory and involving the latter in the testing process in the acceptance test zone allows us to legally issue factory test reports.