Производство электрощитового оборудования
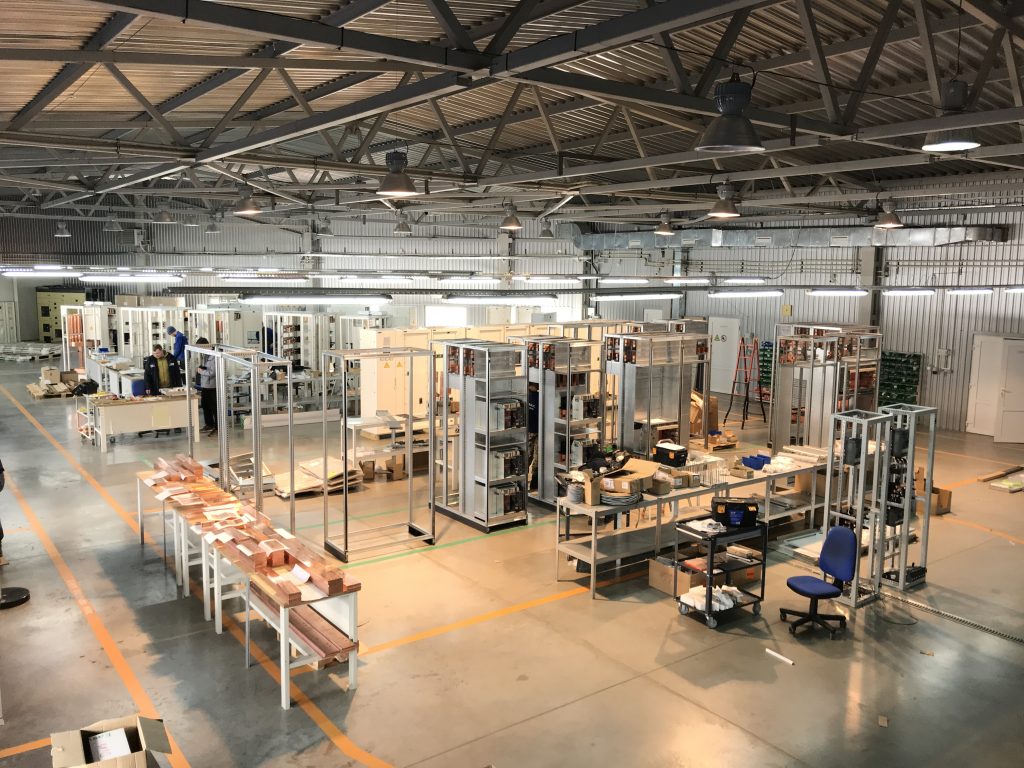
Производственная часть компании «Концерн «Ксимекс» играет особую роль, поскольку воплощает в материи потребности заказчика, инженерно-творчески воплощённые на «бумаге» нашими конструкторами. Чем более сложная, новаторская или масштабная задача ставится, тем более высокий уровень ответственности ложится на наших конструкторов и монтажников.
Следуя принципам «Если хочешь сделать хорошо, сделай это сам» и «Если задача не противоречит законам физики – мы её решим», наша компания поэтапно и целенаправленно развивала собственные производственные мощности, начиная с 1998 года, и на сегодняшний день реализовала более 1200 проектов различного назначения и сложности. В основе наших проектов лежит оборудование ведущих мировых производителей, в частности, нашего главного партнёра компании Schneider Electric.
На производственных и складских площадях боле 2000 м.кв. сегодня трудятся несколько десятков высококвалифицированных и опытных работников, имеющих все необходимые допуски и сертификаты.
Это позволяет нам выпускать электрощитовое оборудование самых разных назначений, начиная от щитов ВРУ и АВР для жилищного сектора до силовых распределительных щитов на токи до 7300А для промышленности, щитов специальных назначений, выполняемых согласно отраслевых стандартов, для морских применений и щитов собственных нужд подстанций, в том числе АЭС.
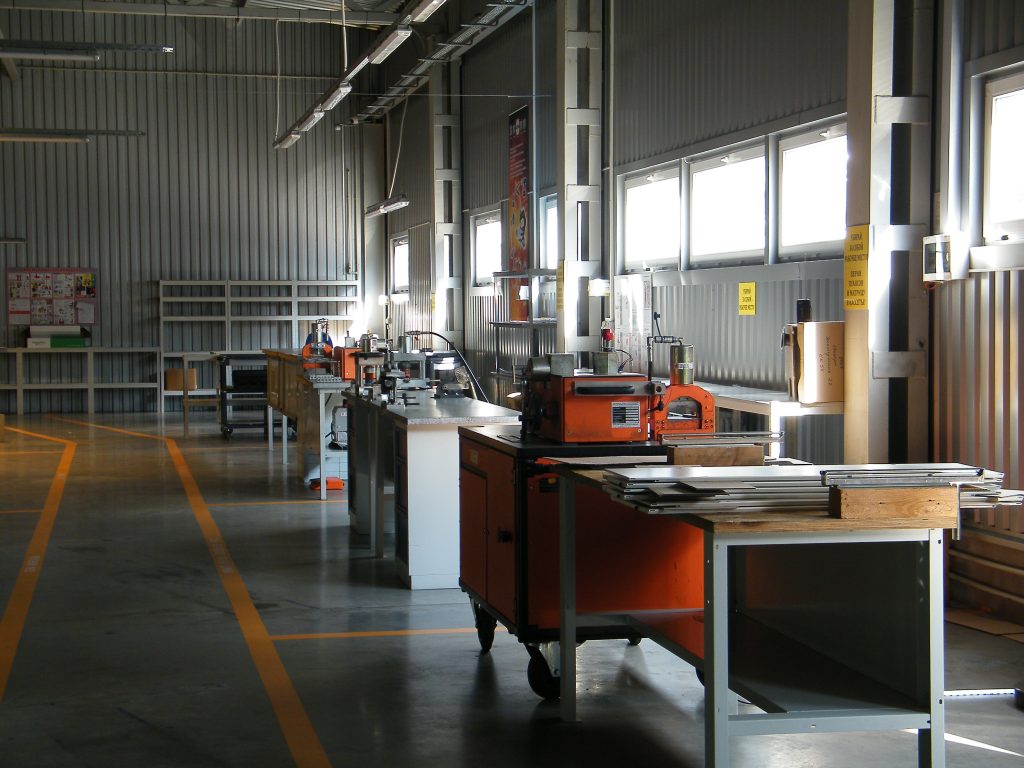
Для получения продукции необходимого качества, мы используем металлы ведущих европейских производителей. В основе любого силового распределительного щита всегда присутствует токопроводящая часть электрической цепи. Мы используем исключительно высококлассную электролитическую бескислородную медь классом чистоты 99,9%. Кроме того, для обработки такого материала используем специализированное гидравлическое оборудование от ведущих компаний, таких как Alfra и ERICO.
НАДЁЖНОСТЬ КАК КЛЮЧЕВОЙ ФАКТОР
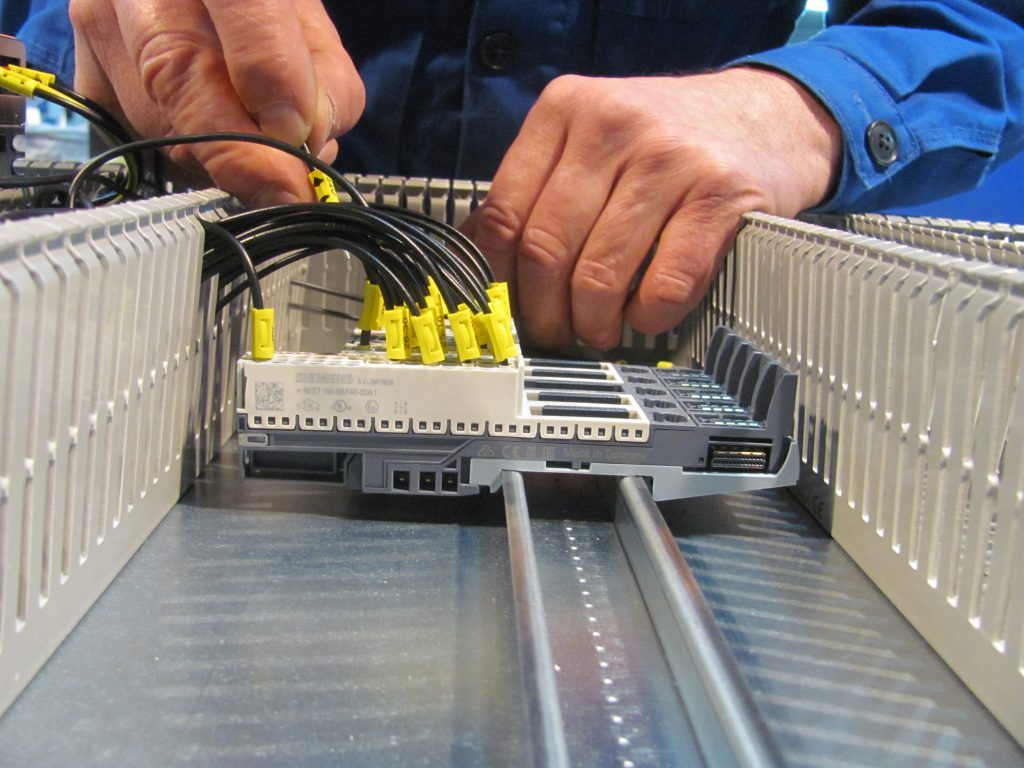
Современные электроприемники, независимо от сферы деятельности (жилые, промышленные или объекты инфраструктуры), требуют надежность и гарантию стабильности питающей сети, которая в основном характеризуется чистотой питающего напряжения, бесперебойной его подачей и гарантированной защитой потребителя от внешних факторов.
Это крайне важный аспект, поскольку большинство аварий и неполадок приходится именно на ту часть цепи, которая является последним рубежом. Именно эти участки требуют наличие надежного защитного и коммутационного оборудования, установленного в такие же надежные и проверенные техническими лабораториями конструктивные решения.
В связи с этим, проектирование, выпуск и наладка надежных электрораспределительных щитов и шкафов управления, адаптированных под требуемую задачу, не является чисто формальным и простым решением. «Гаражная сборка» такого рода оборудования не дает защиты конечного потребителя (электроприемника), с высокой степенью вероятности не способна локализовать аварию и более того, следующий по этапу защит аппарат и устройство (электрощит) может не отработать корректно и не отсечет аварийный участок, что приведёт к негативным последствиям как для остальных потребителей, так и для себя самого в целом. Зачастую, неправильная работа и несогласованность цепей защит по всему участку линии, находит «узкое», более слабое место, которым может являться именно этот «гаражный щит», в последствии становящейся очагом распространения аварии или пожара как в доме, так и на предприятии.
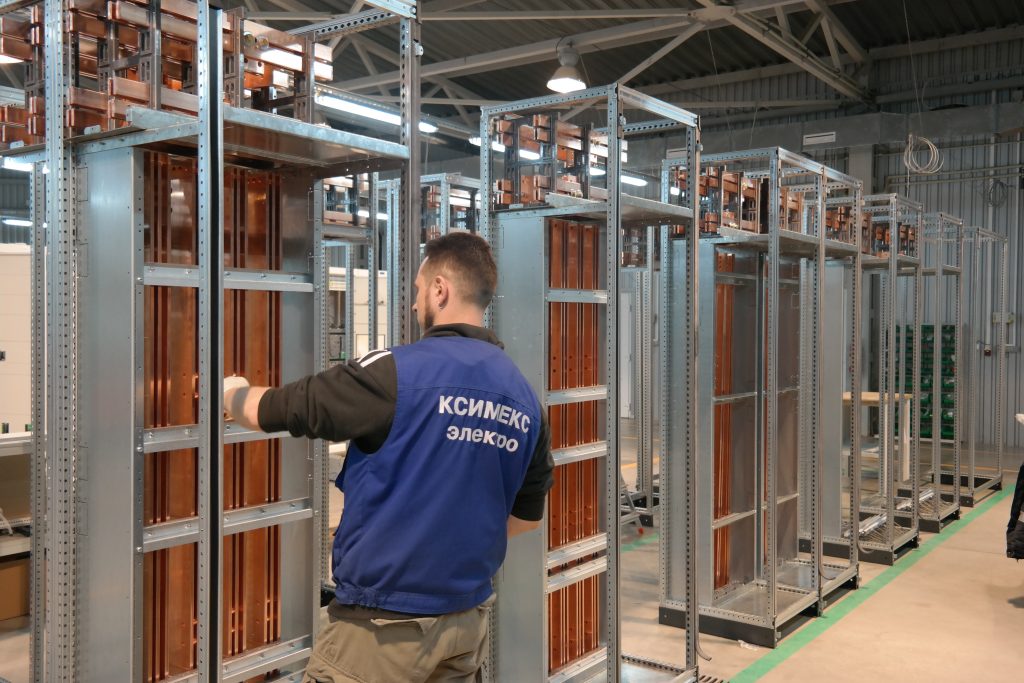
Лицензионное оборудование защиты, распределения и управления – это гарантия стабильности и надежности любого промышленного или жилого здания, а комплексное решение с применением защит от поражения электрическим током – это гарантия сохранения человеческой жизни. Наш опыт позволяет нам с уверенностью заявлять, что мы способны профессионально решать такие задачи.
КОНТРОЛЬ КАЧЕСТВА КАК ГАРАНТИЯ НАДЕЖНОСТИ И ДОЛГОВЕЧНОСТИ
Начиная с 2003 года у нас на предприятии действует и постоянно совершенствуется система контроля качества, сочетающаяся с современными методами производства. Ежегодно проводятся аудиторские проверки независимыми специалистами одной из ведущих европейских компаний с мировым именем, которые подтверждают высокий уровень культуры производства. Это позволяет нам выпускать продукцию в срок и с необходимым уровнем качества.
Структура производственного процесса по сборке электрощитов построена на строгом алгоритме прохождения всей продукции по четко регламентированному маршруту:
Вся поступающая на производственный участок продукция подвергается тщательной проверке. Аппараты защиты и коммутации проверяются на целостность, работоспособность и соответствие заявленным электрическим характеристикам. Проверка аппаратов происходит не только по цепям управления, но и прогрузкой первичными токами. Прогрузочные стенды предприятия позволяют провести комплексные проверки токами до 16000А.
Оболочки электрических шкафов, все комплектующие необходимые для сборки, панели и механические части проходят первичную проверку на отсутствие внешних повреждений, а движущиеся части на механическую работоспособность.
Приборы измерения, индикации и учета после входного контроля передаются на проверку в органы метрологии для прохождения аттестации и получения подтверждающих документов. Обнаружение элементов, не удовлетворяющих заявленных заводом-изготовителем характеристик, отправляются по рекламациям производителю для замены на кондиционные. Данный этап проверки является очень важным на этой стадии, т.к. выявленные недостатки в комплектации и работоспособности полученного оборудования не могут сыграть отрицательную роль в срыве сроков выхода готовой продукции. К выходу готового изделия все оборудование по рекламациям поступает на производство и подвергается новым испытаниям.
В процессе сборки изделий, департамент технического контроля (ТК) постоянно находится на сборочном участке, вносит обнаруженные замечания в лист контроля качества в процессе сборки. Департамент ТК принимает готовое изделие из зоны монтажа только в том случае, если все обнаруженные в процессе сборки замечания были устранены, отметки об устранении внесены лицом, осуществляющим сборку данного изделия. На предприятии постоянно действующая система KPI (Key Performance Indicator) т.е. все обнаруженные замечания в процессе сборки фиксируются в отдельном журнале регистрации.
Данная методика регистрации позволяет определить степени профессиональной подготовки специалистов, акцентировать внимание на повторяющихся ошибках, принять меры к устранению последних. Персонал конструкторского и монтажного участка проходит постоянные обучения и усовершенствования как на территории Украины, так и на европейских заводах и учебных центрах. Перенимаемый опыт европейских коллег внедряется на производстве и в инженерных направлениях.
Готовая и проверенная на этапе сборки продукция (электрический щит), поступает в зону приемо-сдаточных испытаний. Доступ персонала, принимающего участие в сборке данного изделия становится строго ограниченным. За проверку берутся специалисты департамента технического контроля. Проверка готового изделия на соответствие конструкторской документации, комплектность, целостность силовых и контрольных цепей, комплекс проверок с подачей повышенного напряжения, проверка соответствия заявленных степеням защиты (IP), подача напряжения и имитация всевозможных отклонений от стандартных, отслеживание действий автоматики и выходных параметров в зависимости от входных данных. Регулировка аппаратов защиты на требуемые значения срабатывания устройств защиты, привязка систем управления щита к требуемым параметрам входных значений. Окончательная проверка работы всех элементов входящих в состав готового изделия и оформление протокола проведения испытаний с отметкой о прохождении или возврату на доработку оборудования. Только положительно пройденные проверку изделия разрешаются к упаковке и перемещению на транспортировочную зону.
Наличие собственной аттестованной электротехнической лаборатории и привлечение последней к процессу испытаний в зоне приемо-сдаточных испытаний, позволяет нам законно выдавать протоколы заводских испытаний.
Все изделия, прошедшие сборку и получившие положительное заключение департамента ТК на возможность упаковки и отгрузки, проходят этап контрольного взвешивания и упаковки. Все габаритные изделия, предназначенные для поставки в раздельном состоянии, упаковываются и взвешиваются отдельными погрузочными местами. Комплект поставляемого изделия такого типа сопровождается упаковочным листом, содержащим перечень всех поставляемых отдельно единиц изделия, инструкциями по монтажу на объекте, вспомогательными элементами фиксации на время транспортировки и дополнительными упаковочными защитными элементами. Комплектность и состав упаковки зависит от способа поставки (транспортировки), возможных вариантов хранения на строительных площадках или транспортных контейнерах.
Погрузка и поставка оборудования выполняется в строго оговоренные Договором сроки. Упаковка, маркировка, погрузка в транспортные средства, а также фиксация в грузовых транспортных отсеках полностью контролируется отделом логистики. Если имеется такая возможность, в точке разгрузки присутствует представитель нашей компании.
В случае монтажа на объекте оборудования, сторонней монтажной компанией, наша фирма предоставляет услуги по проведению шефмонтажных работ. Группа наших специалистов присутствует на строительной площадке, контролирует процесс монтажа и подключения щита. Осуществляет технические консультации и вносит рекомендации для соблюдения всех моментов целостной сборки готового изделия. Осуществляет финальный контроль правильности сборки и подключения щита на объекте. Присутствует во время первого пуска. Устанавливает щит на гарантийное обслуживание.
По желанию заказчика и учитывая важность объектов как нового строительства, так и реконструируемых предприятий. Компания в состоянии предложить увеличенные сроки гарантийных обязательств, дополнительных условий сервисного обслуживания, дистанционного мониторинга работоспособности изделий, осуществлять бесплатную послегарантийную техническую поддержку и консультации специалистов предприятия Заказчика.